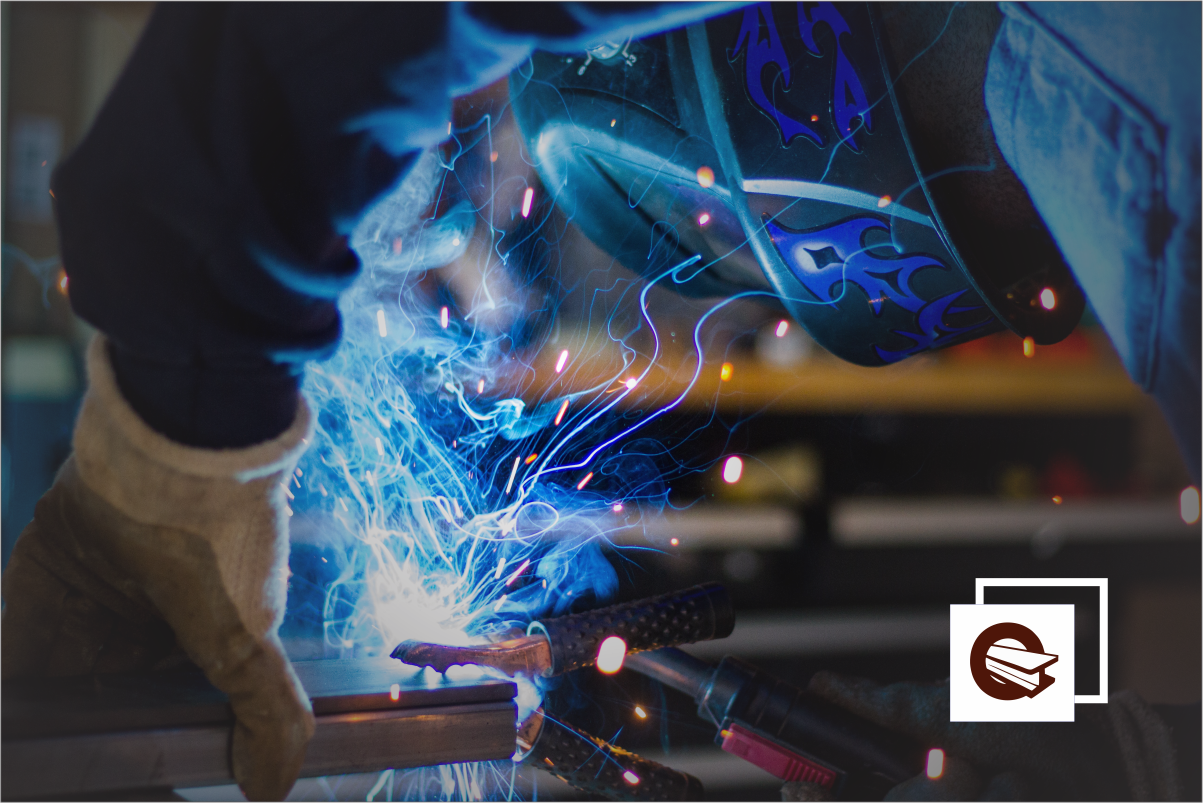
In theory, welding in an industrial environment is similar to other types of welding. It entails combining high temperatures, pressure, and occasionally filler material to make two distinct components continuous with one another. This enables contractors to secure pipe assemblies, replace heat exchangers, and do a variety of other installation and maintenance tasks.
While welding is a straightforward process in theory, there are various complications involved. Because of these welding obstacles, such as contamination, numerous welding procedures have emerged, each with its own purpose, optimal circumstances, and perfect welding surface.
Read our guide to five distinct types of welding services and the welding process in general to learn more about various sorts of welding services for industrial manufacturing.
1. Shielded Metal Arc Welding
Shielded Metal Arc Welding (SMAW), sometimes known as stick welding, is a widespread and classic industrial welding technique. In this scenario, the “stick” is an electrode that conducts electricity into the base material, melting it to link two components together.
The electrode is surrounded by a flux coating, and when it warms up during operation, both the electrode and the flux coating progressively melt. This flux coating provides the shielding mentioned in the name—as it melts, it forms a shielding gas that keeps impurities at bay.
This steadily melting electrode and flux give a steady supply of shielding, ensuring that your project is never contaminated.
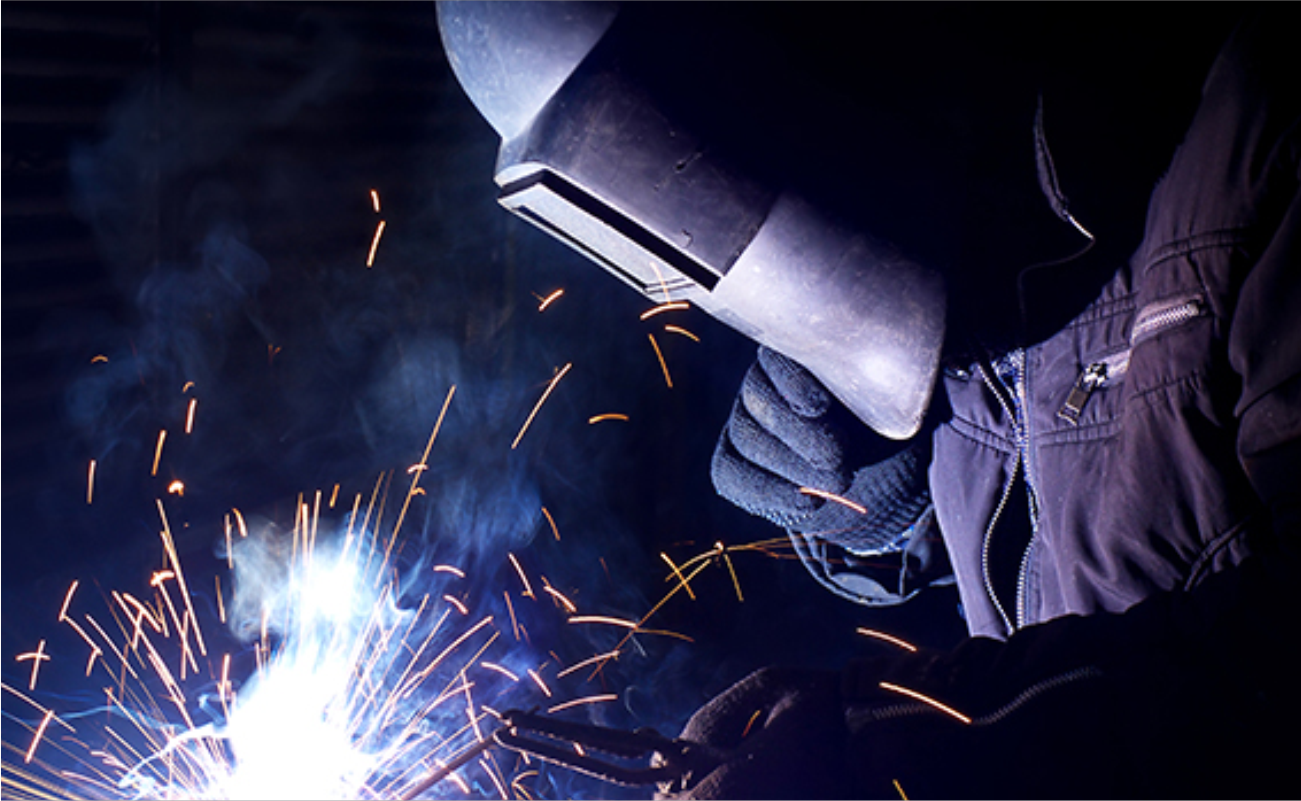
Stick welding is very beneficial for corroded metals or regions that have not been thoroughly cleaned. Furthermore, while this is a versatile technique that can be used for a wide range of industrial applications and materials, it is best suited for thick, substantial metals and is not suitable for welding thinner metals.
2. Gas Metal Arc Welding
Meanwhile, Gas Metal Arc Welding (GMAW) is an alternative with some significant distinctions to stick welding. Gas Metal Arc Welding (also known as MIG welding for metal inert gas) is similar to stick welding in that it employs an electrode that progressively melts onto the base material during operation.
In contrast to stick welding, the GMAW electrode lacks a shielding flux covering. Welders use an external shielding gas, usually inert helium or argon gas, to compensate for the absence of shielding. Metal Active Gas (MAG) welding, like GMAW/MIG welding, pumps in external gases, but these are a combination of oxygen, carbon dioxide, and argon.
This welding procedure is best suited for joining thinner metal components such as sheet metal or tube. Furthermore, GMAW is excellent for interior welding and needs you to carefully clean the foundation surface before working.
3. Gas Tungsten Arc Welding
Gas Tungsten Arc Welding, or TIG, which stands for tungsten inert gas, is another sort of welding service for industrial manufacturing that is sophisticated and difficult to learn. To prevent contamination, tungsten welding, like GMAW, requires an external shielding gas and extensive preemptive cleaning.
Unlike other welding processes, TIG welding does not need the continuous incorporation of filler material. Welders use their welding torch to join bigger metal components while manually feeding a filler rod that matches the base surface material with their other hand.
They can exclude the filler if they are working with thinner, more delicate metals. Due to tungsten’s extraordinarily high melting point, the TIG welding electrode does not melt away during welding, unlike other procedures.

Overall, TIG welding needs talent and experience to acquire, but when learned, it produces clean and exact welds. Manually introducing filler gives an expert far greater control, as does the shorter tungsten electrode, making it an ideal welding procedure for exterior areas that must be flawless.
4. Flux Cored Arc Welding
Another welding process is flux cored arc welding (FCAW). FCAW is a development of the MIG and SMAW methodologies. Instead of a flux-coated filler like SMAW, Flux Cored Arc Welding uses filler with a tube of flux material at its center, hence the name.
FCAW comes in two varieties: self-shielded Flux Cored Arc Welding (FCAW-S) and gas-shielded Flux Cored Arc Welding (FCAW-G) (FCAW-G). FCAW-S requires no additional shielding beyond that provided by the flux core when it melts and forms a barrier. FCAW-G, on the other hand, integrates both the flux and the external gas shielding.
While this method is often more expensive, it is a considerably quicker welding alternative than MIG and SMAW. It is also more consistent and reliable, and it does not lose efficacy as environmental circumstances change. Consider FCAW, especially if you have a thick metal that requires extensive penetration for optimal coalescence.
5. Submerged Arc Welding
Submerged Arc Welding (SAW), unlike many other welding techniques, is a mechanical rather than a manual procedure. Engineers establish the specifications for a weld and then let it run automatically, which requires exceptional precision before it can be executed.
Furthermore, Submerged Arc Welding is called “submerged” because the technique covers the surface with a granular blanket of flux before the wire electrode reaches any weld spots. Because the granular flux covers the whole surface, you cannot see the electrode actively fusing the metal components during this process.

The objective of this flux is to completely insulate it from pollutants. Because the flux blanket prevents extraneous chemicals from entering, experts do not need to employ shielding gas as they would with other welding procedures.
The advantages of SAW include quick, even deposition and limited room for human mistake if properly designed. Though its automation is an advantage in general, it does restrict the number of potential weld places accessible. SAW is a good choice for controlled, circular welds around a pipe or other cylindrical component, as well as straight line welds, due to its mechanical nature.
Itís hard to find knowledgeable people for this topic, however, you sound like you know what youíre talking about! Thanks
Excellent article. I definitely appreciate this site. Keep writing!